Health and safety in the workplace has transformed drastically since its conception in 1833. Today’s health and safety is characterized by government agencies, all-encompassing legislation, and continuous improvement, resulting in a gradual decrease in accidents over time.
Of course, accidents still occur and this would continue to be the case even if you wrapped every single employee in cotton wool. But many businesses continue to experience accidents well above the national average and end up paying for incidents that could easily be avoided.
This doesn’t have to be the case and there are best practices businesses can immediately implement to help improve workplace health and safety. Interested? Then keep reading to find out what causes workplace accidents and how you can prevent them.
Quick navigation:
- How do accidents impact your business?
- What causes accidents at work?
- How to prevent accidents in the workplace
How do accidents impact your business?
When a workplace accident occurs, it has far-reaching consequences that extend beyond the immediate employee injury. In any workplace accident, there are two types of costs: direct and indirect costs.
Direct costs
In most cases, the direct cost is simply the worker’s compensation. The average cost of a workplace injury claim is $40,000. That cost alone is enough to break smaller businesses. However, costs don’t end there.
Indirect costs
Indirect costs are what happens outside of direct compensation. Unlike direct costs, providing an exact number is difficult as costs can vary greatly depending on the industry and business model. Indirect costs are often much higher than direct costs. Below are just some examples of indirect costs:
Loss of productivity - regardless of your industry, losing an employee will result in a loss of productivity. Your team may be forced to take on additional responsibility as well as maintain their usual standard when performing their own tasks—something that isn’t sustainable over the long term. Or if that isn’t the case, then you’re simply losing the production of your injured team member.
Recovery of lost production - can include overtime pay, hiring costs, and adjustments made to accommodate the injured worker.
Employee replacement training - in most instances the injured employee needs replacing. The average cost of training a new employee is $1252.
What Causes Accidents at Work?
There are a lot of reasons why accidents occur. Some are common across all workplaces, and others might be entirely unique to your company.
OSHA defines a workplace accident as an unexpected event with a negative outcome. It also provides a comprehensive list of workplace hazards that could lead to accidents.
If you work in construction, then check out our construction safety risks blog (it comes with a free safety checklist!).
How to Prevent Accidents in the Workplace
The types of workplace hazards will vary depending on your industry. However, there are some best practices all businesses can implement to reduce the number of workplace accidents.
1. Risk Assessments
A risk assessment is the process of identifying what risks and hazards exist or may exist at some point, how they may cause harm, and what steps can be taken to minimize them. It’s a legal requirement for all companies.
HSE provides a useful video on how to conduct an effective risk assessment.
Not only do risk assessments save lives, but they also save money by preventing fines and can reduce a company’s legal liability.
2. Regular Inspections
Regularly inspect equipment and machinery to ensure everything is functioning correctly and avoid accidents via malfunctions. For an industry like construction, where heavy machinery is widely used, regular inspections can save lives.
You should also inspect dangerous activities and processes to assess risks and decide whether an alternative and safer method can be used.
For a more thorough breakdown, check out HSE’s page on workplace inspections.
3. Ongoing and Effective Training
Preventing accidents is a lot easier when every member of your workforce possesses the knowledge and skills necessary to mitigate risks.
Health and safety training is a legal requirement for every business. However, nowhere does it say that it must be effective. Some businesses treat training as nothing more than a box-ticking exercise. Others have good intentions but employ traditional long-format training that doesn’t promote engagement and knowledge retention.
For those that are serious about reducing accidents, consider a more progressive training format that’s tailored to the modern worker. Mobile-learning is being increasingly adopted among industry leaders as it provides engaging and informative content to workers when they need it most. In fact, mobile learning is shown to improve knowledge retention by 55% and increase engagement by 72%.
And because workers can access safety information on the job in their time of need, safety practices become more consistent, resulting in a stronger workplace safety culture.
Try a sample eduMe lesson on how to lift objects safely, either click through the lesson below or scan the QR code to access it on your phone.
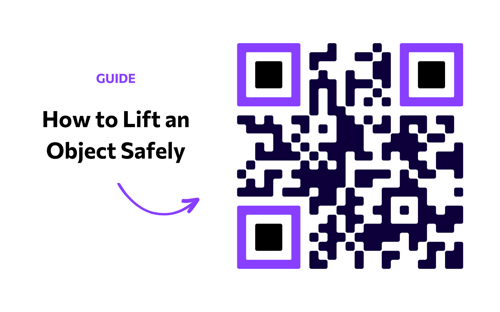
4. Personal Protective Equipment (PPE)
PPE is protective equipment worn to minimize exposure to workplace hazards. PPE may include hard hats, gloves, high-visual clothing, and face masks.
It has proven to be very effective in reducing injuries. Hard hats were worn by only 16% of workers who sustained head injuries, and only 1% of approximately 770 workers who experienced face injuries were wearing the recommended PPE.
OSHA recommends the implementation of a PPE program that should address hazards and train employees on the use of PPE.
5. Clear Signage
Clear signage, or safety signage, should be provided when risks can’t be avoided or controlled in any other way.
Employers are responsible for training their employees to understand what all signs mean and what action they need to take when seeing a sign. Additionally, safety signs must be properly maintained—a few missing letters can change a sign’s entire meaning.
HSE provides safety sign guidance for employers.
6. Accident Reporting
Accident reporting will help you evaluate the effectiveness of the measures you have put in place to avoid workplace hazards. It will also help you improve your workplace health and safety by allowing you to investigate accidents and determine what went wrong.
Employers should provide some level of training to ensure workers know how to report an accident. Although the process will differ from place to place, a general rule is to make the process efficient and accessible. A time-consuming and complex process will only deter workers from reporting incidents.
7. Physical Assessments
Many of the prevention methods up until now have focused on evaluating the working environment and equipment. However, it’s equally important to assess your workers to make sure they’re fit to perform the tasks involved effectively and without risk to their own health and the health of others.
With physical assessments, employers should consider the why and when. Why is the assessment needed? A common example is when an employee’s health condition may impact their ability to effectively do their job (e.g. a musculoskeletal condition that prevents heavy lifting).
When is an assessment needed? This could be when an employee is returning after extended time off due to illness. Or a new recruit is starting a physically demanding role.
8. Encourage Communication
Some businesses fail to include their workers when developing and improving their workplace health and safety. Yet these are the people directly impacted by your practices and can offer valuable insight into what does and doesn’t work.
Create a culture of open communication and feedback from your workforce. We recommend using surveys as they’re easy to disperse to your employees, they can be tailored to your needs, and the results are easy to collect and evaluate.
We’ve listed a lot of practices that your business can implement. But where to start? We recommend starting with eduMe, a mobile-training platform that seamlessly integrates into existing worktools and provides an effective way to engage and educate your workforce.
Find out how Flagger Force, a leading short-term traffic control services company reduced their injury incidents by 60% with eduMe - read the case study "eduMe has exceeded our expectations. It has revolutionized our training and really enhanced our overall communications platform." Tamara Palmer, Internal Communications Manager, Flagger Force |
Want to watch a short video on how eduMe works? fill in the form below to see a pre-recorded demonstration 👇